BCase 1
BCase 1 Is My First Custom Computer Case.
BCase 1 is my first custom-designed computer case, engineered and manufactured entirely from the ground up. This project combines the thermal performance of a mid-tower or larger case with the refined aesthetics and premium materials often found in compact mini-ITX cases like the FormD T1 and the Fractal Terra. By scaling up dimensions while retaining the overall form and optimizing airflow, BCase 1 strikes a perfect balance between performance and design.
Following the initial assembly and component installation on tyhe prototype, I identified a few areas for refinement. After making adjustments to the cut file, I’ve ordered the final version to be precision-cut by SendCutSend out of thicker material, addressing the limitations of the thinner material and imprecise plasma cutter used in the prototype. The results so far have been impressive: the prototype achieved a reduction of 10–15°C in CPU temperatures and 10–20°C in GPU temperatures compared to an ITX case, bringing its cooling performance in line with mid-tower and full-tower ATX cases.
With a focus on efficient design for manufacturing, BCase 1 is constructed from just two halves plasma-cut from 2.5mm 5052 aluminum in the final version, requiring only four 90-degree bends. This streamlined approach allows a single person to complete the manufacturing process in just a few hours, with the majority of the time spent on sanding and finishing. As a result, production costs and timelines are significantly reduced compared to competing cases, enabling more affordable pricing, greater availability, and faster time to market.
Takeaways
Manufacturing the final prototype by hand allowed me to thoroughly explore the production process and identify potential challenges, as well as the limitations of both machinery and materials. The initial prototype was constructed from millimeter-thick material, which proved prone to warping when plasma cut. This issue was resolved by switching to 2.5mm thick material for the final product.
The bottom half of the prototype was originally made from sheet steel for its rigidity and magnetic properties. However, the added strength was unnecessary and only increased weight, cost, and production complexity. As a result, I opted for an all-aluminum construction in the final model, offering a better balance of strength, weight, and simplicity.
The first iteration used a shallower, vertical layout with an "Icebox" airflow system, which filled the case with cool air and allowed components cool themselves and eject the exhaust air out of the case, however this design proved too large and size inefficient during cardboard modelling. this lead me back to the drawing board, where i experimented with component configurations until i managed to half the total size, and remove the need for an expensive riser cable in the process. The final design also features a more inclusive GPU intake.
Unlike many ITX cases that rely heavily on mesh for airflow, I chose a more ATX-inspired cooling system. By closing off most of the case, this design enables precise control of airflow pathways. The GPU and CPU coolers draw fresh, cool air directly through their heatsinks and into the case, where it is efficiently expelled by case fans positioned at either end. This approach has proven to be highly thermally efficient, reducing fan speeds, noise levels, and overall power draw.
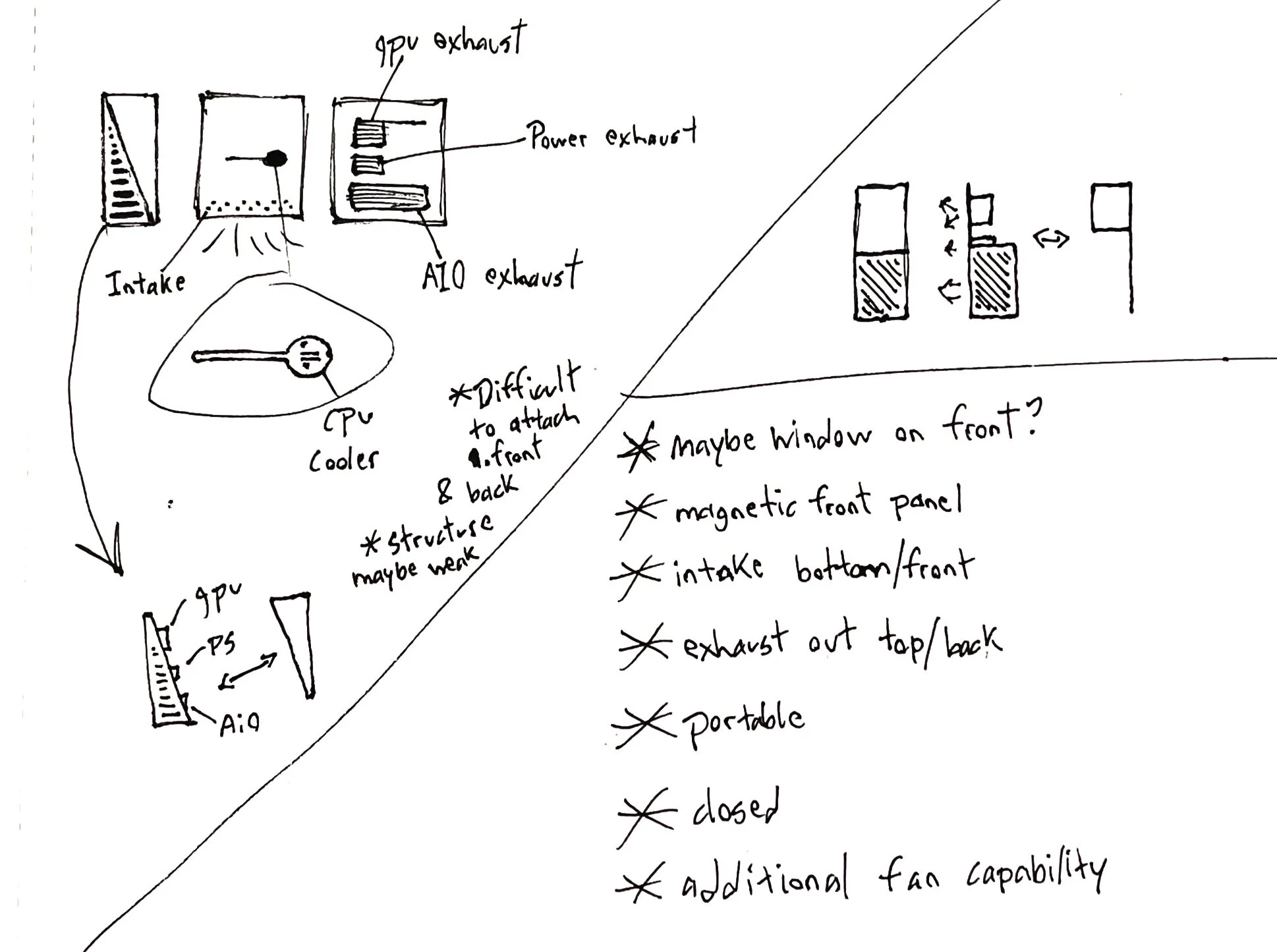






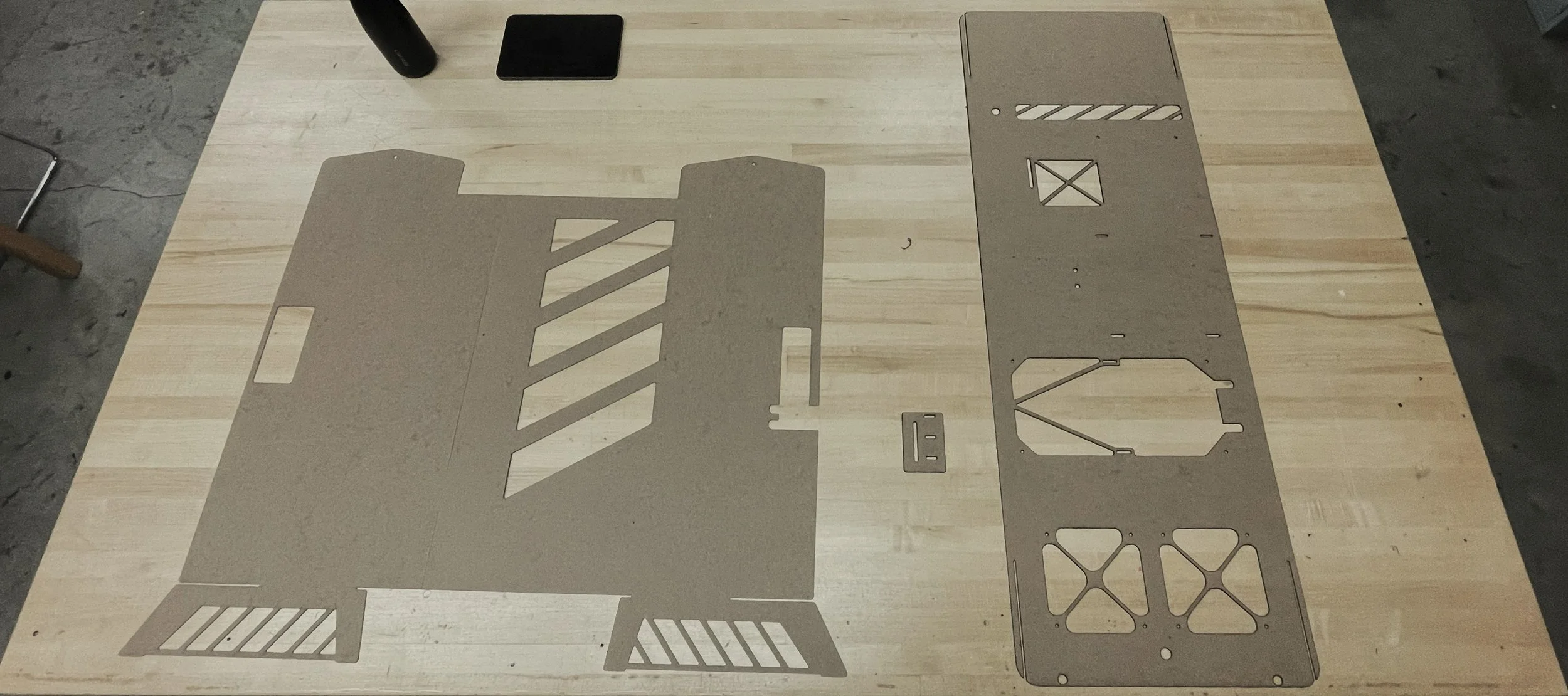
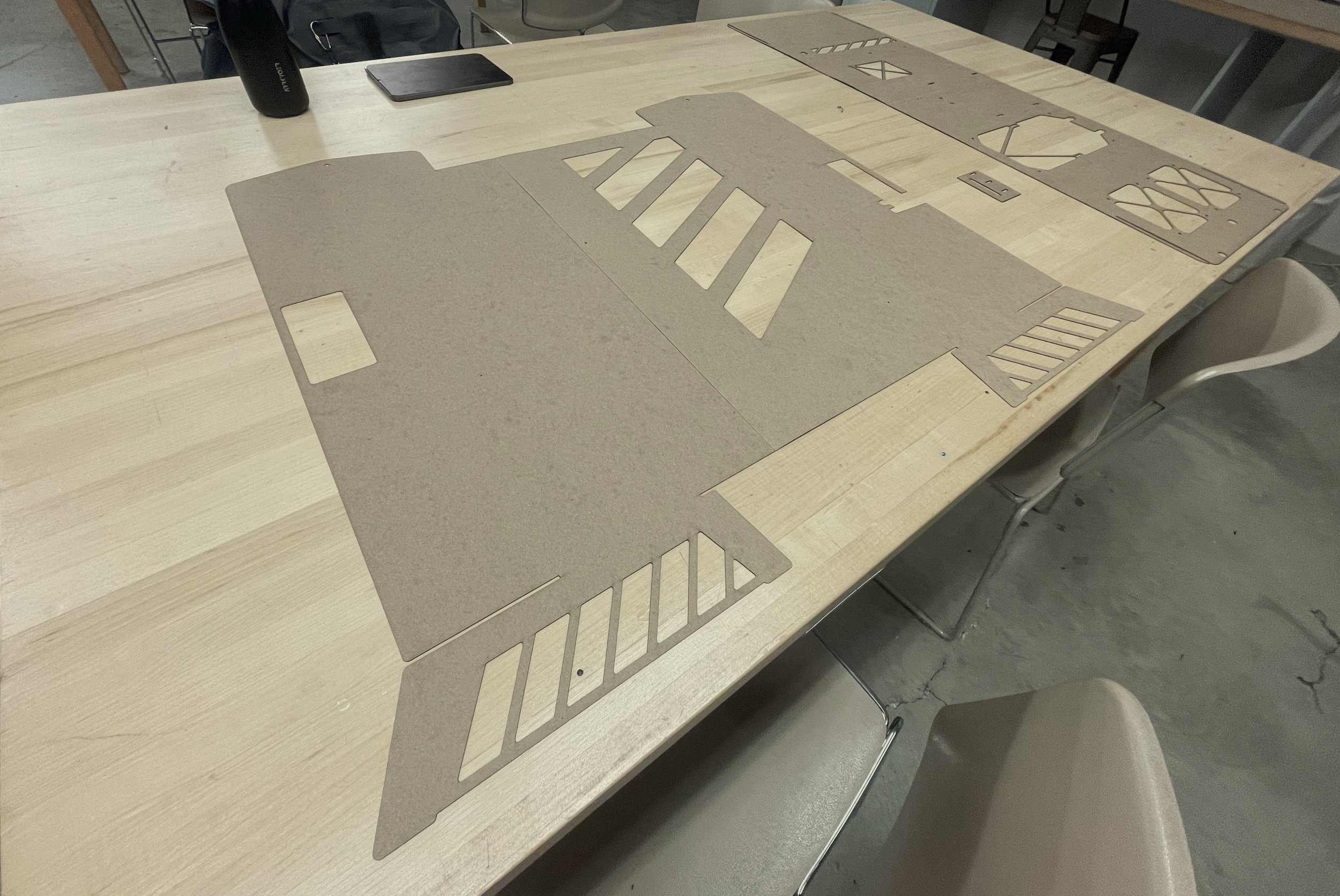
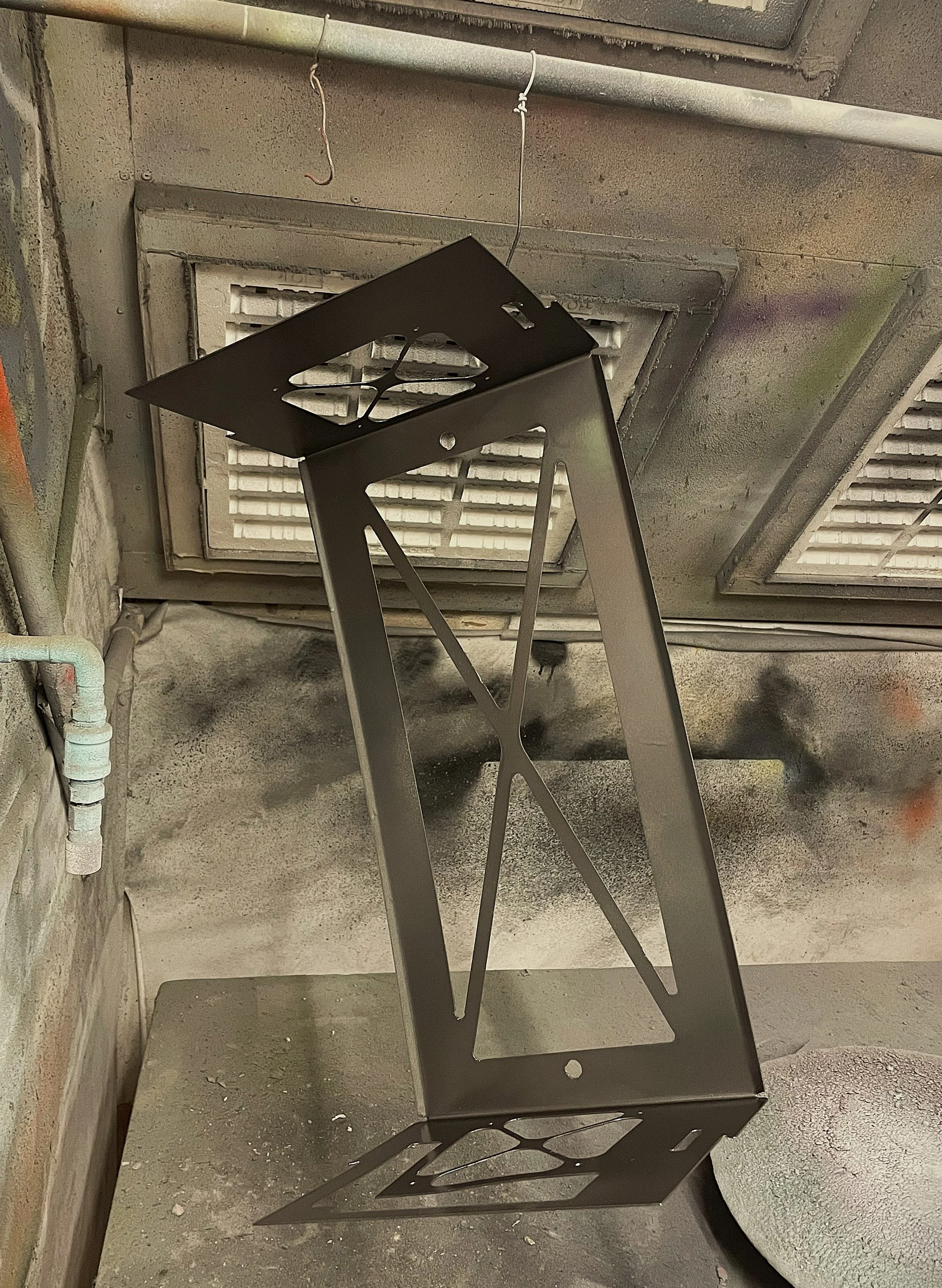
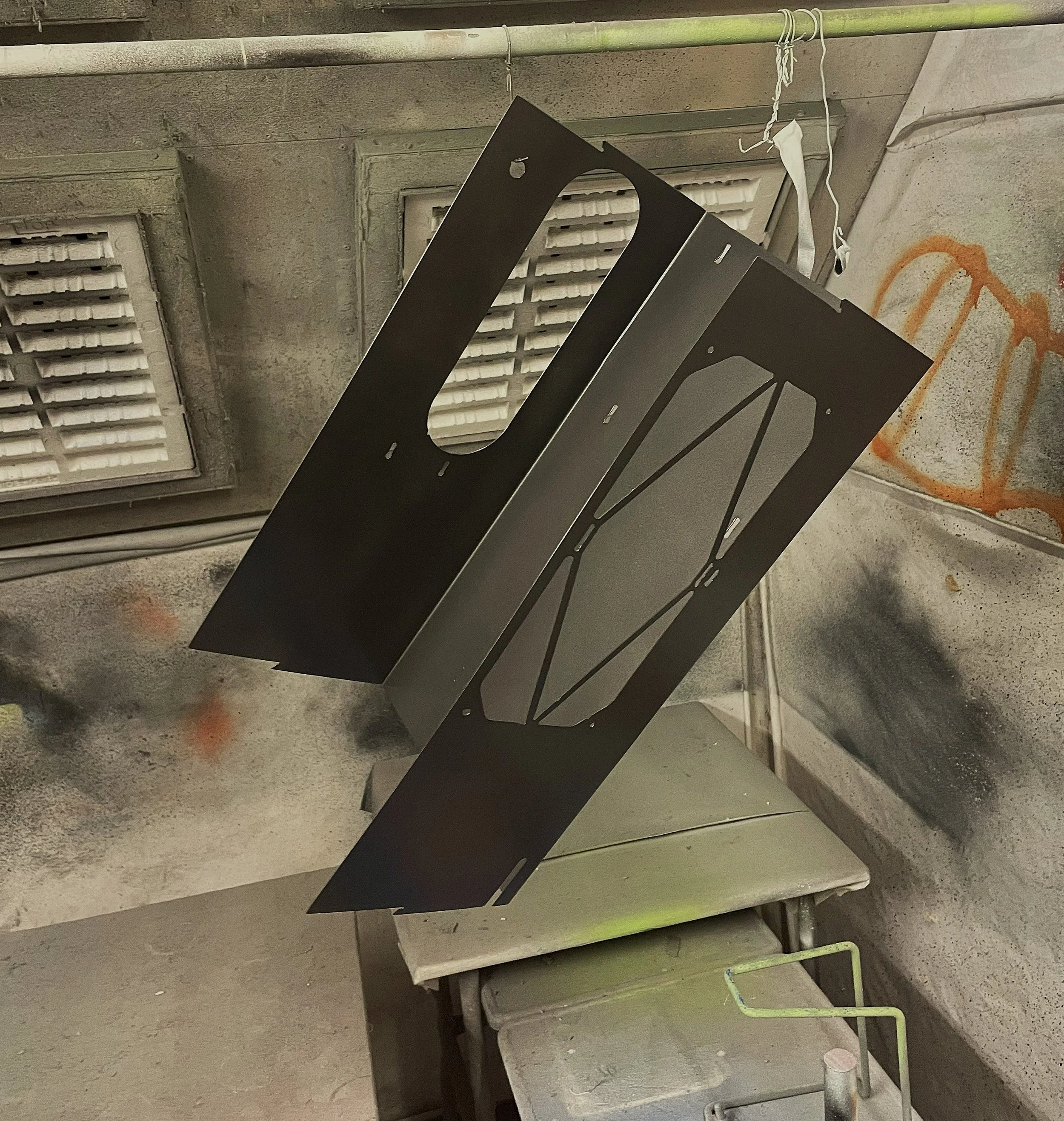
